Roper Whitney Brakes
Connecticut Floor Brakes
Optional Accessories
Automatic Folding Machines
Roper Whitney has been producing quality folding systems for a variety of markets. The Autobrake integrates advanced design with professional-grade performance.
It combines automated bending of angles up to 145°, material clamping, and material support into a single CNC-controlled wing-bending system.
- Reduced labor costs
- Improved part accuracy
- Reduced setup time
- Minimized tool changes
- Improved part quality—especially on soft and pre-painted materials
Features
Integrated Sheet Support & Material Handling: Automatic sheet positioning, high-speed backgauge fingers, and servo motor-driven ball screws for accuracy within ±0.004”.
Automatic Dual Clamping System: Programmable pressure accommodates various materials and hem types with no tool changes.
Construction: Rigid welded steel frame, shock-absorbing end stops, and precision-machined folding beam for consistent results.
Crowning System: Manual center crown adjustment improves bend accuracy and allows for radius bends.
Intelligent Controls: The Synergy CNC system allows for offline programming, 3D simulation, USB backup, DXF imports, and more.
Optional Accessories
Kombi Beam: Adds box folding capabilities and quick-change tooling. Available on most Autobrake models (except AB1016).
Available Models:
- AB1016: 10’ x 16 ga mild steel
- AB1014, AB1214, AB1212, AB1011, AB1009 — all with optional Kombi Beam
Manual Brakes
Connecticut Floor Brakes
Precision manual bending brakes with features like adjustable apron hinges, removable nose bars, tie rods for rigidity, and a wide range of sizes for different material capacities.
Models: 816 (8’ x 16 ga), 1018 (10’ x 18 ga), 1016 (10’ x 16 ga)
Connecticut Bench Brakes
Rugged USA-made brakes for box and pan or straight bending. Models include U416 for 16 ga steel and U422 for 22 ga and lighter. Adjustable for a wide range of radii and includes apron stop rod, handles, and counterweight.
Image Gallery
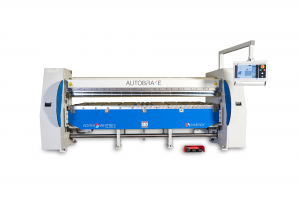
AB1014K Autobrake with Kombi
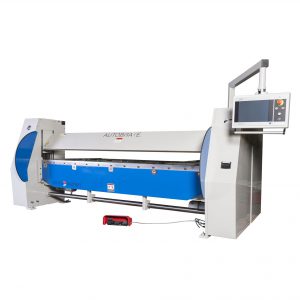
AB1016 Autobrake
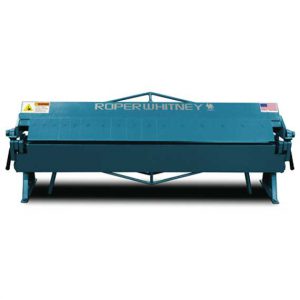
Bench Brakes
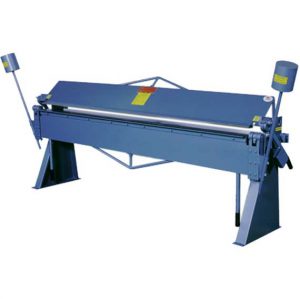
Floor Brakes
Need help selecting the right Roper Whitney brake?
Contact our team or request a quote today.